Manufacturing Process our polypropylene woven products production process
Ganpati Plastfab's manufacturing process of woven polypropylene woven bags and FIBC bulk bags and PP jumbo bags use only pure virgin polypropylene resins, and every bag is quality checked before being packed and shipped. Complete quality management systems are strictly followed at each step of the manufacturing process. This includes tape extrusion, fabric weaving, extrusion lamination, gravure printing, bag forming, bag sewing, quality testing and customer shipping. We strive to keep up with the latest requirements of woven polypropylene sacks and FIBC bulk bags to ensure our customers receive the highest international quality products.
Extrusion & Winding
High speed extrusion, double stage draw, tape stretching and winding lines incorporate state-of-the-art technology to produce PP/HDPE tapes. The lines are designed to meet the highest performance and quality requirement with maximum efficiency and flexibility while using minimum raw material and energy.


Fabric Weaving
High performance circular loom machines are used for producing circular fabric of PP/HDPE tapes with almost zero defect. Circular looms for PP fabric weaving are a combination of latest technology with advantages of lower energy consumption. They meet the widest range of fabric specifications, maximizing productivity and optimizing cost.


Bag Conversion
High speed bag conversion lines are used for producing bottom folded and sewn woven sack made from roll of tubular woven PP/HDPE fabric. These new generation machines are suitable for conventional bag application and designed for cross cutting the tubular fabric, bottom folding, sewing and stacking. Their state of the art automated functions result in consistent quality of cut and sewn bags.



Multi Filament Yarn
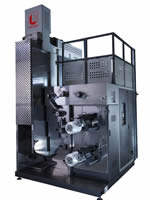
FIBC Production
FIBC production requires special purpose machines for production. State of the art high performance automatic fabric cutting machines with the option of spout or profile cutting. Hydraulically operated baffle panel or profile or hole cutting machines capable of cutting profiles or round cut-outs as per requirement. Webbing or belt cutting machines needed to be cut belts to required lengths to make lifting loops for the FIBCs.

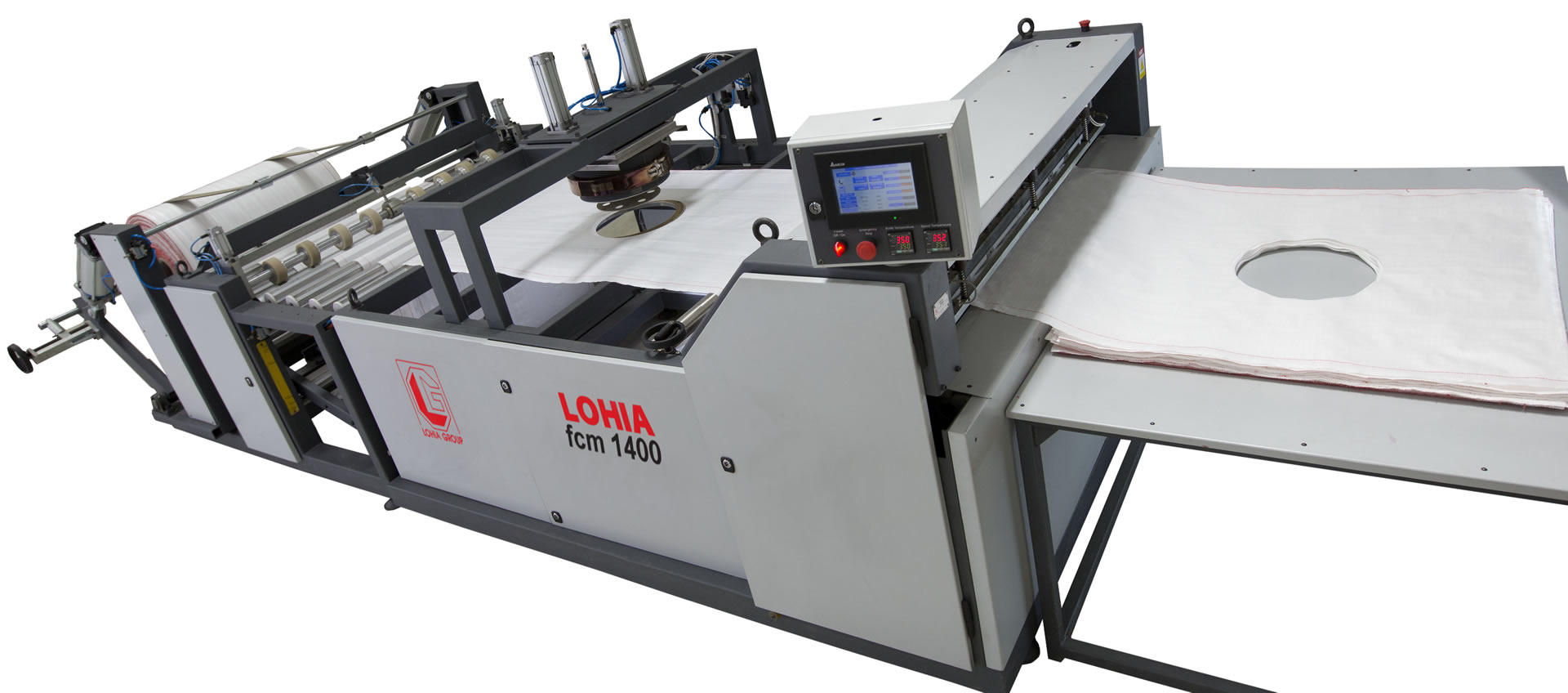

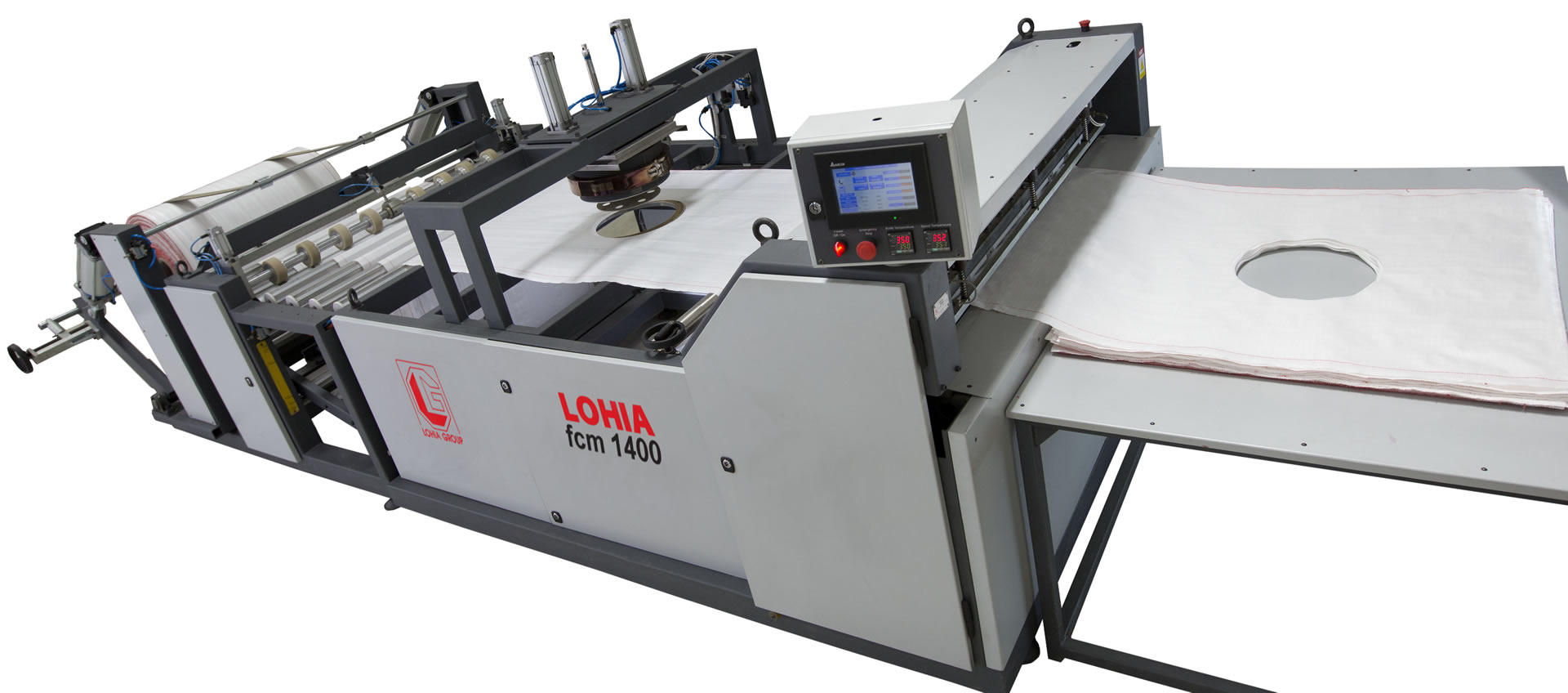
Testing & Packing
All requisite laboratory equipment are utilised for quality checks at each stage of production to ensure flawless quality to the customers.
Bags are checked, sorted and stacked for proper shipping to customers. Hydraulic pallet and bale press for systematic and cost efficient storage and transportation, the finished bags should be pressed and packed properly for protection.
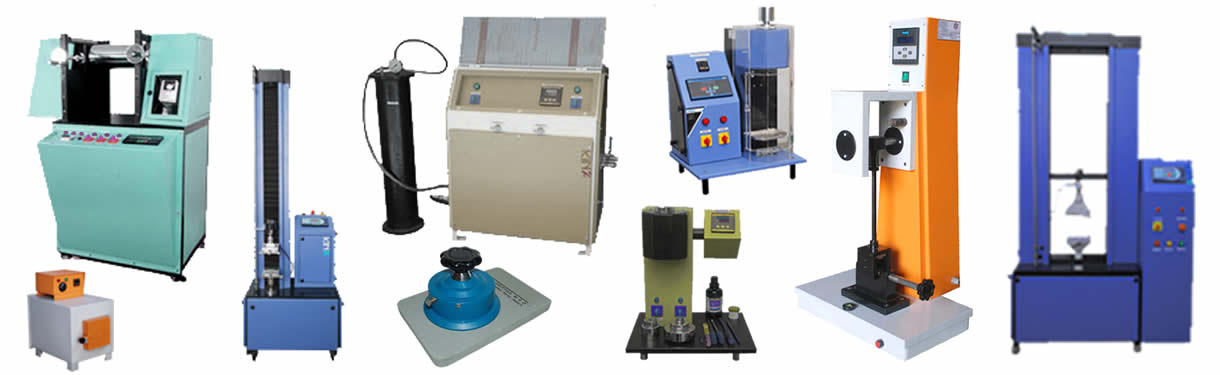

Bags are checked, sorted and stacked for proper shipping to customers. Hydraulic pallet and bale press for systematic and cost efficient storage and transportation, the finished bags should be pressed and packed properly for protection.
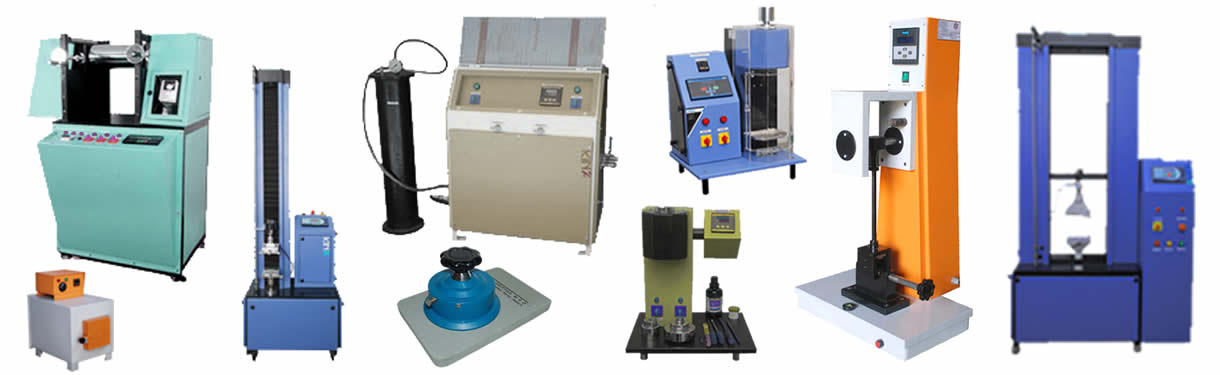
